Sintering technology
Particularly suitable for medium and very large production runs
Unlike conventional metallurgical processes, which always involve the solidification of a molten metal, sintering starts with a metal powder.
Around 1908, the first self-lubricating rings appeared. Then, in 1935, the automobile industry began to use sintered mechanical parts.
Powder metallurgy, or sintering, can be used to produce parts with high geometric precision, from a few grams to several hundred grams, and capable of withstanding high mechanical stress.
Sintering is particularly well suited to medium and very large production runs.
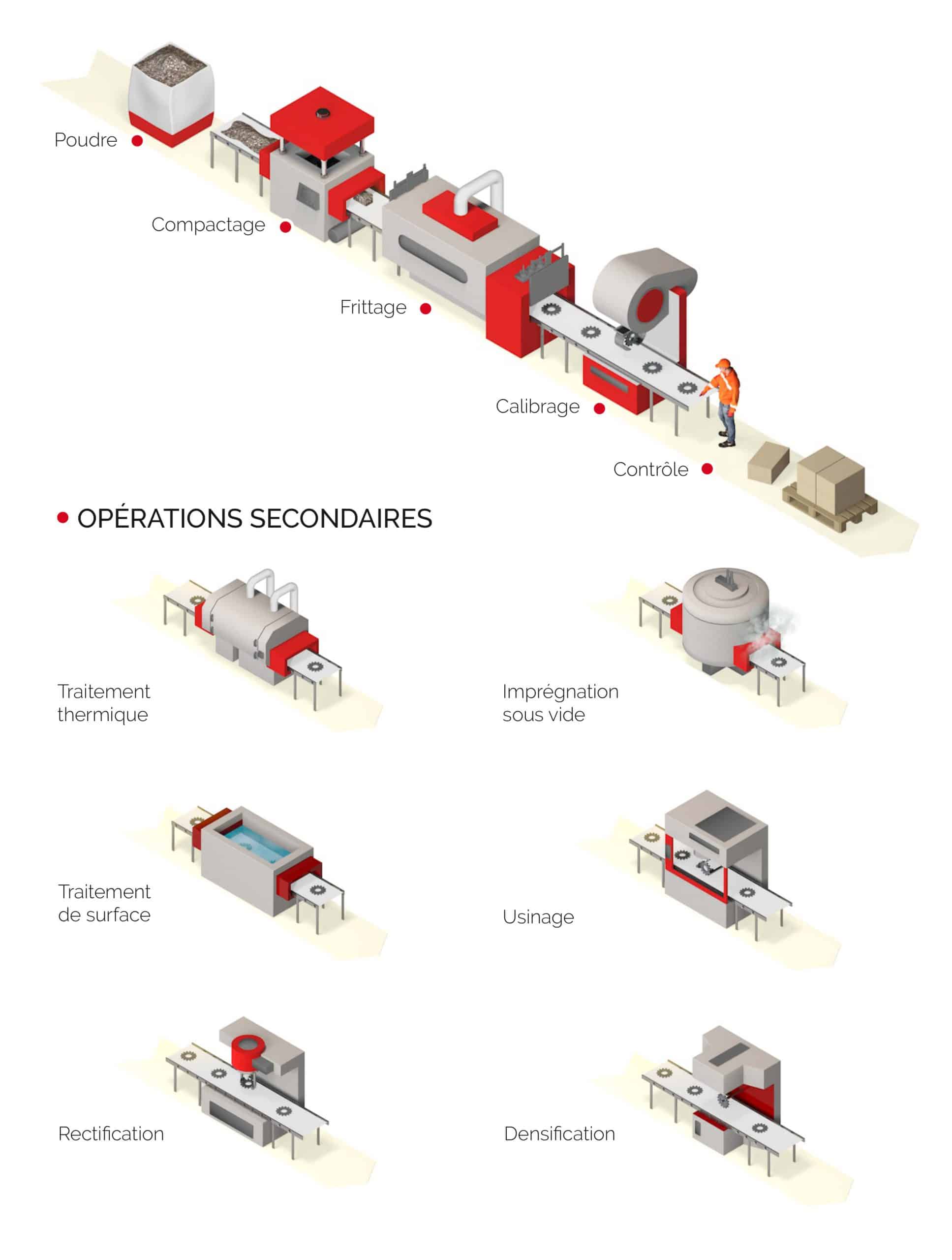
Compaction or Compression
Presses can be mechanical, hydraulic or electric, with the choice of power depending on the part to be compacted. At Porite, power ratings range from 0,5T to 1,600T.
Compaction tooling is gravity-filled. It consists of a matrix (external geometry of the part) of upper and lower punches. Their number will depend on the design of your part and the type of press used. This first operation will give the part its geometric shape, but without the required mechanical characteristics (green part).
Sintering
From a practical point of view, the sintering operation must meet three requirements:
- Give the compressed part the required mechanical properties (resistance, hardness).
- Maintain maximum dimensional accuracy (nominal dimension and tolerances).
- Be as economical as possible.
Sintering temperatures are between 1120°C and 1135°C. Some parts require high temperature sintering from 1200°C to 1350°C, under a protective atmosphere.
Sintering temperatures are typically between 1120°C and 1135°C. Some parts require high-temperature sintering at 1200°C to 1350°C. The sintering atmosphere is adapted to the part material.
Sizing
The sintering operation generates an increase in dimensional dispersion and shape defects.
If the sintered part no longer meets the required specifications, a calibration press may be necessary.
Secondary operations
- Machining
- Correction
- Deburring
- Densification
- Thermal treatment
- Surface treatment
- Impregnation
- Vacuum impregnation