MIM-Metal Injection Molding
Le MIM, pour répondre à la complexité de vos designs dans l’industrie du frittage
Le MIM (Metal Injection Molding) consiste à fabriquer des composants métalliques plus ou moins complexes par injection d’un mélange de poudre métallique et de liant polymère thermoplastique, appelé « Feedstock ». Ce mélange est transformé en granulés, puis injecté dans un moule.
Le déliantage, ou élimination des liants, peut se faire de manière thermique ou chimique, et cette opération peut prendre jusqu’à 24 heures. Le frittage est ensuite réalisé dans un four, soit continu sous atmosphère protectrice, soit sous vide.
Le MIM utilise des équipements similaires à ceux de l’injection plastique. Cette technologie est particulièrement adaptée à la production de pièces de moyennes et grandes séries à la géométrie complexe.
Chez Porite, nous avons débuté la fabrication de pièces MIM à Taiwan en 1996. Nos secteurs d’activité principaux sont l’outillage électroportatif, l’électronique, l’automobile et l’industrie mécanique. Nous injectons divers types de matériaux, principalement des poudres à base de fer et d’inox.
N’hésitez pas à nous consulter !
Le procédé
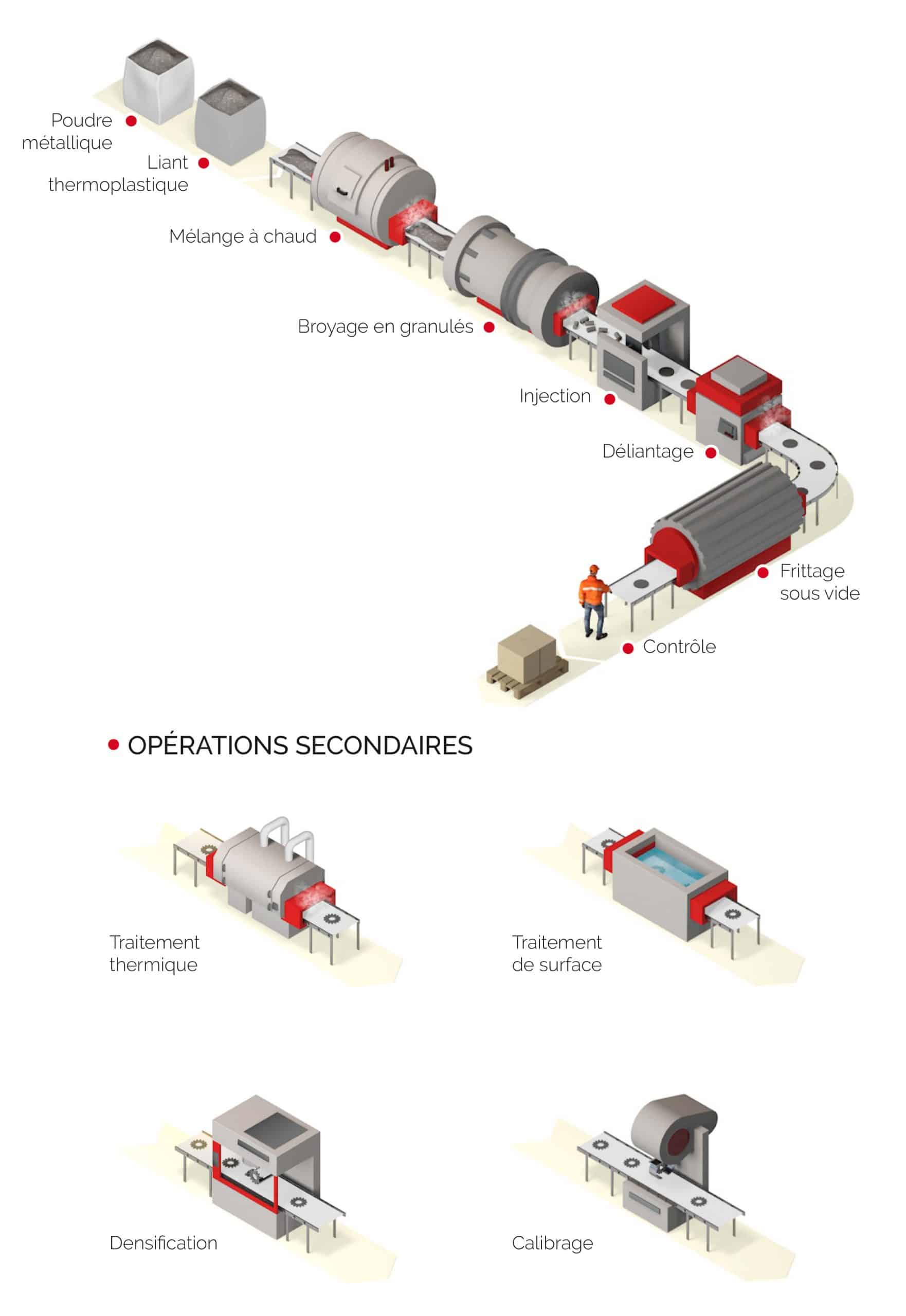
Une alternative à d’autres technologies
Les avantages du MIM
- Production de pièces complexes : Permet de fabriquer des géométries complexes difficilement réalisables par d’autres méthodes.
- Réduction des opérations d’usinage : Contrairement à d’autres technologies, comme la cire perdue, le MIM minimise le besoin d’usinage supplémentaire.
- Densité élevée : Obtenue de 95 à 98 %, garantissant des propriétés mécaniques proches de celles du métal massif.
- Amélioration des traitements de surface : Meilleure adhésion des traitements de surface anticorrosion par rapport au frittage traditionnel.
- Possibilité de taraudage ou de filetage direct : Permet l’intégration de ces opérations dès l’injection, réduisant ainsi les étapes de production.
- Grande liberté de conception géométrique : Permet de concevoir des composants aux formes très variées et complexes.
- Excellentes tolérances dimensionnelles : Tolérances précises de l’ordre de +/- 0.5 %, garantissant une grande exactitude de fabrication.
Ces avantages font du MIM une technologie idéale pour produire des pièces de haute qualité à des coûts compétitifs.